IForgeIron Blueprints
Copyright 2002 - 2007 IFORGEIRON, All rights reserved.
BP1014 Bloomery Process
by Mattias Zwssler
This article that explains the ''bloomery process'' was written for the IForgeIron readers by:
Matitias Zwissler Engineer for Metallurgy
58256 Ennepetal
Peddenode 3
Germany
Phone 02333-602920
Mobile 0137 5244 992
He spend most of his time on this subject and forging knives and mosaic pattern welding, and demonstrated the whole process twice.
Every one that want to have more explanations is invited to call or write him and will be happy to answer questions.
Bloomery furnace + the process
Origon: beginning of the iron age
Purpose: reduction of iron ore to iron.
Oven design
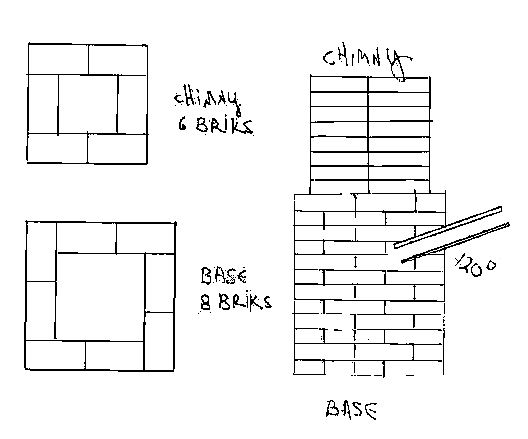
Vertical shaft 12x12 '' the base and the chimney 8x8 height approximately 4'
Ingredients : iron ore (any iron oxide) scale will do. But not (sulfuric ore fes2 ) charcoal +air
In total 70% 12 kg iron oxide in this case scale
15% sio2 quartz sand
15% caco3 kalk
Air 180 litter a minute with a pressure of 0,5 bar 7.5 psi
Process time 8-10 hours
The furnace is built out of heat withstanding brick sand a ceramic pipe out of allu oxide or any other ceramic material the od of the pipe is 1.5-2'' Drawing is attached the ''blowpipe'' seats in the base construction at i20 degrees before the last brick of the ''basement''
Starting the furnace
Fill in charcoal up to the level of the blowpipe and ignite fire then fill it up to the top with charcoals put the air on and on top of the charcoals put on cup of the ingredient mixture, wait until the charcoal is burning down one layer of bricks you fill it up again with charcoals and on top one cup of the scale ingredient mixture and repeat again and again for 8-10 hours.
Chemistry
Air +charcoal o2 +co=co+co2
Oxygen and charcoal react to carbon monoxide + carbon dioxide. At the temp of 1100 and more degrees c 2100 degrees F, we will have only co carbon monoxide which is the reduction gas.
The process is called boudouard process.
Ore reduction
Fe2o3 +co ----->feo+co2
Feo +co --------> fe + co2 ( gas)----> that lives into the air
The bloomery furnace reduces ore to iron in the ''chimney'' and in the ''basement'' the iron particles are fire welded to a ''bloom''
Tips and tricks
Break the iron ore into ''powder''
Break the charcoal into 1'' particles
Add the minerals (sio2, caco3) to get an easy smelting slag
By looking into the pipe you can see the temp you have to maintain a temp of 1200 degrees C, 2200 f
Physics of the ''bloomery'' furnace
Reducing iron oxide by diffusion controlled reaction with co2. The ''speed '' of diffusion is a function of the temp and time and the surface of materials.
The product
The result is a spongy piece of iron with inclusions of charcoal, ore and dirt. It has to be forged out and fire welded on the anvil better with a striker.
Hope the process is clear.
Mattias Zwssler
Thanks to Mattias Zwssler that gave me, showed and guided me, along this beautiful process and wrote the information for IForgeIron.
Uri Hofi
Kolbermoor Conference Germany
Bloomery furnace Smelting (wooz)
by Mattias Zwssler
This article that explains the ''bloomery process'' was written for the IForgeIron readers by:
Matitias Zwissler Engineer for Metallurgy
58256 Ennepetal
Peddenode 3
Germany
Showing the raw material and the final product, the wooz, and some samples forged as a test.
Building the furnace, the air blast ceramic pipe, and the compressor.
Crushing the charcoal to smaller pieces to get a bigger surface and getting more heat with less air. Fill the furnace half, put in the pipe, and turn the compressor on and fill to the top. On the top put a full serving size spoon fo the crushed "scale" iron oxide and the additives.
IRON OXID 70% 12 kg
QUARZ SEND SiO2 15% 2 kg
LIME (CHOLK) Ca Co3 15% 2 kg
From this amount we get at the end of the process 40% - 50% steel to forge.
The process takes 8-10 hours. While burning the charcoal it is sinking down. When it goes down on brick, we fill it up again with the crushed charcoal and on top one serving size spoon of the mixture.
After 8-10 hours we start the process of opening the furnace from the bottom. This is done in the night and the show is spectacular.
After the bloom is out it is taken to the anvil to forge it with two strikers to squeeze it a bit because it is spongy. Then cut it to the wanted sizes of pieces and it is then forged with the air hammer.
Cutting to the desired size pieces and forging to get the steel ready for multi-layers forge welding.
The process is a reduction process.
BEST REGARDS
URI
Recommended Comments
There are no comments to display.
Join the conversation
You can post now and register later. If you have an account, sign in now to post with your account.