
Dean O Riordan
-
Posts
57 -
Joined
-
Last visited
Content Type
Profiles
Forums
Articles
Gallery
Downloads
Events
Posts posted by Dean O Riordan
-
-
I NEED HELP!!!
ok i did the Harding and tempering the other night, and to night i started to polish it, First i had to remove the scale from the steel which i found to easy, any way i got the blade all smooth and sharp and wanted to test it out even thou it not finished. so i cut some paper all was good so far but when i chopped into a piece of wood and then looked at the blade i seen a dint in the blade, now it's not a big dint but a dint that should not be there.
now i did the very same thing as i did when i hardened the last knife, but for some resin the blade is just not hard as the last one
So does anyone know why this is and is there anything i can do to fix it ?
Oh i used old engine oil to cool the blade in.
PLEASE HELP ME
Here is a pic of the dint.
Oh the only thing that i did do different this time is i use my gas forge i made to harden the blade,last time i use the coal forge -
wow very nice knives you have made, i love the last one. very good workmanship.
-
nice bowie cant wait to see it finished
Thanks, i can't wait to get it finished
This is only my 3rd forged knife iv made so far, the first one i made which i still have, was not very good looking.I used an old file to make the blade and then i got lazy and used a wooden file handle for the handle, the seconded one i made which you might of seen in one of my last post, was much better BUT the handle did not go very well with the blade, the handle looked good and the small 4" blade looked good but together not good
This time i thing iv got it right and iv gone all the way with this one, by making all the part's needed to make the knife. -
Just an update tonight i did the Harding on the blade and now it's in the oven. The blade look's ok no sine of crack's so hopefully all is good.
-
very good work, but that is a lot of work to do before heat treat. if it fails heat treatment that was a lot of good work wastedbut 5160 is pretty forgiving, so the likelyhood of success is good.
BTW what kind of wood is that? very nice knife so far, keep up the good work. Ed Steinkirchner
Thank you
The wood is oak, i got some off cut's off a fancy oak staircase on a job i was working on last mouth. -
Hi all,
Okay i am making a new knife and it's the best knife iv made so fay ( well i think so)
The steel i am using is 5160. I have forged out the blade and tang, started the handle made the but cap and hand gard, all i have to do now is harden the blade and then temper it, and polish the blade but it all together file down the but cap until it fit's the shape of the handle.
Here are some pic's of what iv don so far.
The pictures are from the start of the project to what iv don so far.
More to come
I have still a lot of work to do with it but im all most there :D -
Hi all i finished that knife i was making so here are some pic's for you.
and here is a link to a video iv got on youtube.
My video -
Dean
I would temper at 400f for two hours should be around rc60 then let it cool in the oven to room temp. It never hurts to do it twice.
Bob
Cool thanks for the info
Sorry but what dose rc60 mean i tried the search bar but could not fined an answer. -
Stick it in your oven for a few hours at at least 350 degrees Fahrenheit, or maybe 150 Celsius. You need to do it quickly after hardening, I've heard stories of blades randomly shattering from internal stress because the smith waited too long to temper them. Ask someone else for the exact temperatures though, I've only done this once.
Thank you for telling me thatIv put it in the oven to at 350d* F.
Oh do i leave it to cool down in the oven after it's bin in for a few hours, when i tern the oven off ? -
Okay guy's iv just don the heat treat ( Hardening ) of my knife. I used old engine oil, and as far as i can see no sing of crack's the tang is soft but the blade is hard.
Now Tempering of the blade, What's the easy-es way of doing it or the best way of doing it.
lol i stink of burnt engine oil
Here is a picture of the knife. -
Just found out that 5160 steel will not give me the temper line (hamon ) that i would like. so ill have to do with out
Search bar help me out again with this answer
Any way do i use oil for Harding ?
Thanks for the help so far :) -
Like was said it needs to be a shallow hardening steel such as w1,w2 or 10xx.
Yes i use normal furnace cement to coat my blades and it does what i want it to.
Also it need to be a fast quenching oil or water if you choose water be prepared for some broken and cracked blades.
Good luck Bob
I have old engine oil, the steel is 5160.
Thank's -
First: Is it made from an alloy that produces hamons? Most don't.
Then: I know you can use furnace cement; I'm not sure what fire cement in Ireland translates to over here.
Most likely yes if you can get it to stick to the blade.
The steel is 5160 as far as i know it is an alloy steel ( I use the search bar to find out that answer)
It's cut from a leaf spring a very thick one 10mm thick. -
Thank you ever one for the nice welcome, ill give you pictures if that's what you like :D
-
Okay im working on a small knife.I have forge out the basic shape of the blade today and filed down the blade smooth.
Now i am starting to think about the finish on the knife, and would like to have a hamon ( temper line ) on the blade.
Now I know how it is don but what i would like to know could i use fire cement to put on the spine of the blade when Harding it.
Here is a small picture of the knife.
Any help would be of gait help to me.
Thank's. -
-
Oh wow that turned out nice well don.
-
Ive seen a lot of RR track anvils( I have a pretty good one myself) but this is probably the best one ive ever come across..
http://cgi.ebay.com/8-lb-RAILROAD-TRACK-ANVIL-Blacksmith-Forge-N-R_W0QQitemZ120511819284QQcmdZViewItemQQptZLH_DefaultDomain_0?hash=item1c0f106e14
That's a nice looking anvil and well made by the look's of it. -
Since you don't have a link to it yet, here's video4.
You seem to be wetting your anvil and your hammers with water. Is that to cut down on scale?
With you wetstone (oilstone, sharpening stone, honing stone, there's a billion names for them) what kind of oil are you using?
That's shaping up to be a nice sword, keep up the good work!
Thank you,
The stone i am using is an oil-stone.
Well as far as i know wetting the hammer and anvil dose help reduce scale or remove scale from the metal surface.
Here is a link to a website that sell's the same oil-stone i have.
Oil-Stone -
Hi everyone
I found this site last night and spent about 1 hour looking at the site be for singing up, just to see what sort of thing go on here, I came across a lot of very nice work don by other member and hoped that one day ill be as good as them
I am from Ireland a place called Mohill in co,Leitrim ( in the west of Ireland )
Is there any other member from Ireland on here ?
My day job is plumbing and my Hobbes are metal work, i love welding and making thing.
Iv tried making Damascus steel but that did not work out for me
I also made my own coal forge and a gas forge. I also made my own anvil out of a piece of Rail rood track it's not the best but it's doing ok for now. I also made a 10Ton Hydraulic press for forging. I will get some pictures of it soon. -
Hi every one,
I have bin forging on and off for the last year or so, i am by far NO expert on forging. What i think i know is what iv learned as iv gon along
I have tried forge welding and not had much lookwith it yet but plan to try again soon.
I am forging my first Sword and iv bin working on it for about 2 weeks now.
The steel i have used is a leaf spring 2" wide by 1/4" thick, i had to cut down to size be for i could start forging it.
The blade length is 22" long,
The over all length 33" long,
Here is the link's to some videos iv put on youtube
video 1
video 2
video 3
hope you like what iv don so far.
Here is a picture of my first sword i made out of stainless steel
This next picture is of my old sword and the start of my new sword, -
Oh wow that is one nice looking sword you have made.
I am making a sword and it's not 1/2 as good as your sword.
I hope one day i can make some thing as good as that.
Well don.
Damascus steel
in Knife Making
Posted
Hi everyone,
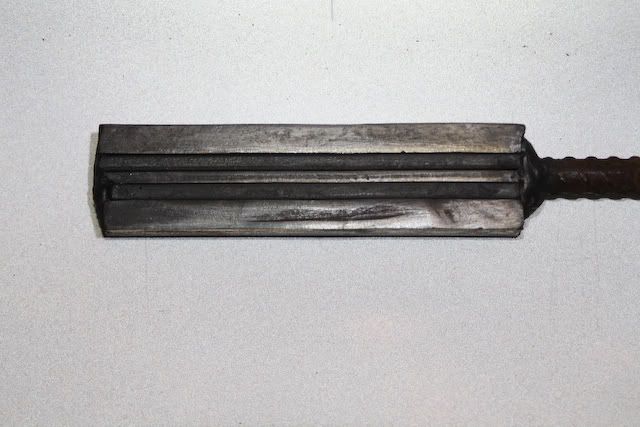
I am going to try and make some Damascus steel, now iv tried this before and not had much luck at it. I have a good idea how it's don and what i was doing wrong before, not hot enough, hitting it to hard.
So iv got my billet made and hope to start on it next week if i am off work.
The steel i am using is 2 bit's of 5160 an old file and 2 bit's of mild steel, here is a pic
Now starting from the top of the billet,
5160
mild steel
old file
mild steel
5160
Do you think this is ok and will it weld together ok ?
All comment's are welcome.